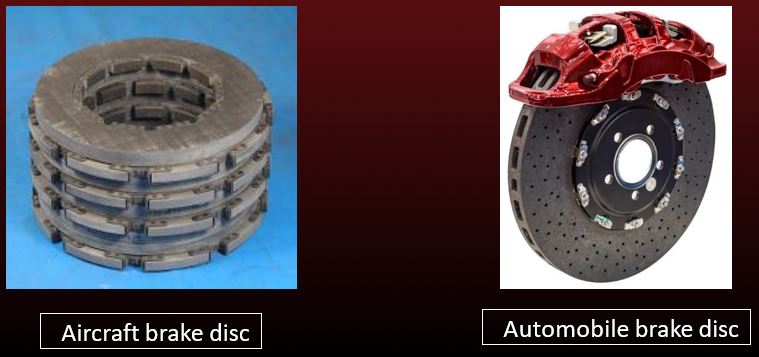
All of our Carbon Ceramic Brake Discs are manufactured from a next-generation Carbon Fibre Reinforced Ceramic (CFRC or Carbon/Carbon), continuously R&D'd over the past several years for our OE clientele (several
major European Brake Manufacturers) and produced in-house using our own proprietary processes, transforming Carbon/Carbon into Carbon/Silicon Carbide (C/SiC) ceramic to create our superior lightweight brake discs. If you've ever driven a European Hypercar or raced in a Porsche with
Upgraded Carbon Ceramic Brakes (not the inferior Brembo/SGL CCM Brakes), there is a very high chance you've experienced our performance and quality first-hand.
Born from the application of commercial & military aerospace derived technology and designed for motorsport applications, carbon ceramic discs provide extraordinary advantages which directly result in increased vehicle braking performance whilst maintaining the same reliability of cast iron discs.
The discs are primarily composed of materials such as silicon carbide (SiC), silicon (Si), and graphite reinforced by carbon fibre. This unique blend results in a material that combines the best attributes of carbon and ceramics.
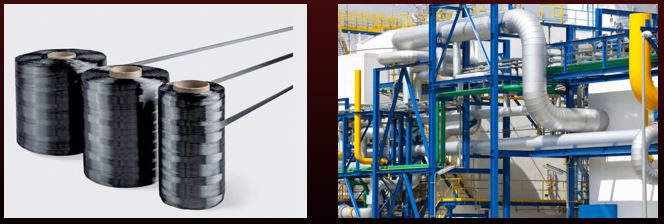
Carbon fibre, also known as graphite fibre, is an advanced material that has revolutionised various industries due to its exceptional strength-to-weight ratio and unique properties. It is a form of carbon with extremely high stiffness and tensile strength, making it an ideal reinforcement material for composites.
While the carbon ceramic discs on most production road cars typically use T300-grade discontinuous (chopped) carbon fibre, CTE interweaves T700-grade continuous (long) carbon fibre to form a 3D multi-directional matrix, producing a stronger and more durable product, helping to keep brake system temperature down with stable & consistent performance.
Brief Manufacturing Process of CTE’s C/SiC Brake Discs
Preform Weaving, Chemical Vapour Infiltration (CVI) and Siliconization are the three key stages of the whole process which determines the disc performance.
3D Preform by Unique Needling of Carbon Fibre
CTE’s brake discs are made using carbon fibre based 3D fabrics which are prefabricated by a needle-punching process. A unique 3D structure of carbon fibre is woven together from multiple layers of continuous fibre cloth to form the base carbon material (preform).
Chemical Vapour Infiltration to form the Carbon/Carbon Material
CTE have developed over the past several years a proprietary Chemical Vapour Infiltration (CVI) method of Ceramic Matrix Composite (CMC) fabrication, whereby reactant gases diffuse into the porous preform to form a deposition.
Deposited material is the result of a chemical reaction occurring on the fibre surface. The deposition fills the space between the fibres, forming a composite material composed of the matrix (the deposited material) and the fibre preform (the dispersal phase).
Additionally, a heat treatment process will be used to initialise graphitization, whereby the preform is heated to 3000°c in order to eliminate non-carbon elements from the preform, rearranging the atomic structure into a highly ordered and dense 3D crystalline structure.
Siliconization by RMI
CTE have developed a proprietary Reactive Melt Infiltration (RMI) process in order to deposit the Silicon Carbide into the Carbon/Carbon material to produce the final composite material – C/SiC.
Melt infiltration is a one-step process for making high-density composites based on low pressure, capillary-driven infiltration of a molten silicon liquid into the porous Carbon/Carbon material.
Surface tension and viscosity of the RMI process primarily determine the infiltration, though geometry of the pores/channels within the preform can have a strong influence on the kinetics of the process.
If you have any questions at all, please feel free to
Contact Us.